
NDT sensor design
Design, modelling and measurement
We have extensive experience in the design of ultrasonic sensors, from the characterization of piezo-electric transducers, to integration into sensors for manual, semi-automated and fully automated applications.
We have developed designs for air-coupled, contact and immersion transducers for NDT inspection, bond testing, and condition monitoring applications.
​
We have experience in the design of passive gimbals for contact, immersion and local immersion; as well as active probe manipulators. Our gimbal designs include analysis of beam angle and offset variation arising from surface adaptation, in order to quantify and minimise the impact on probability of defect detection. We use a range of position sensing and actuation solutions based on the operating envelope, system integration requirements, accuracy and inspection speeds required.
​
We have also designed sensors for magnetic field strength measurement, magnetic flux leakage inspection, and Helmholtz coils for laboratory calibration.
​
Additive manufacturing allows for quick evaluation of design variants, and our in-house 3d printing capability and precision machining offers rapid development from concept to engineered design.
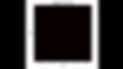
Modelling and characterisation
Quantitative design analysis and validation
We conduct ray-traced and finite-element based modelling of ultrasonic wave propagation to allow optimisation of sensor designs to meet measurement requirements.
​
We carry out vector impedance spectrum analysis of piezo-electric transducer elements to verify wave-mode frequencies and harmonics. Sensor performance can be validated by hydrophone sound field measurement, and transducer characterisation to ISO standards.

Bespoke transducer characterisation systems
For R&D and Production
We provide ultrasonic transducer characterisation systems, integrating a range of ultrasonic pulser-receiver, acquisition and motion control platforms with software tailored to your work flow, budget, and measurement and reporting requirements.
​
Both conventional and phased array contact (angled beam and TOFD) and immersion probes can be evaluated to EN12668:2, BS EN ISO22232:2, ISO18563-2, or Airbus AITM 6-0016 standards and integrated with immersion tanks for automated beam profile measurements.
​
We also carry out high resolution needle hydrophone beam profile scanning, which can be provided as a service or integrated into immersion characterisation systems.

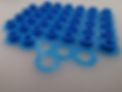
Prototype Ultrasonic probes
With in-house FDM and MSLA 3D printing, 4 axis CNC machining and laser engraving we are able to draw upon our considerable experience of ultrasonic probe design to produce prototype and pre-production ultrasonic probes for various applications. This batch of 50 probes was designed for Lamb Wave based condition monitoring of CFRP structures.
​
We have also designed and supplied OEM probe kits for ultrasonic bond testing applications, including pitch-catch, resonance and MIA mode inspection methods.
